Temperature and Industrial Coatings: A Crucial Relationship
Understanding the relationship between temperature and industrial coatings is essential for anyone involved in the material selection, application, or maintenance of these protective substances. This comprehensive guide delves into why temperature is a critical factor in the effectiveness and longevity of industrial coatings.
What are Industrial Coatings?
Industrial coatings are advanced protective layers applied to surfaces in various sectors, including manufacturing, automotive, marine, and construction. Their primary role is protecting surfaces from environmental damage, wear, and corrosion.
Key Types of Industrial Coatings
Epoxy Coatings: Renowned for toughness and resistance to chemicals.
Polyurethane Coatings: Known for their aesthetic finish and UV stability.
Zinc-Rich Coatings: Excellent for guarding against rust.
Acrylic Coatings: Popular for their fast-drying nature and color retention.
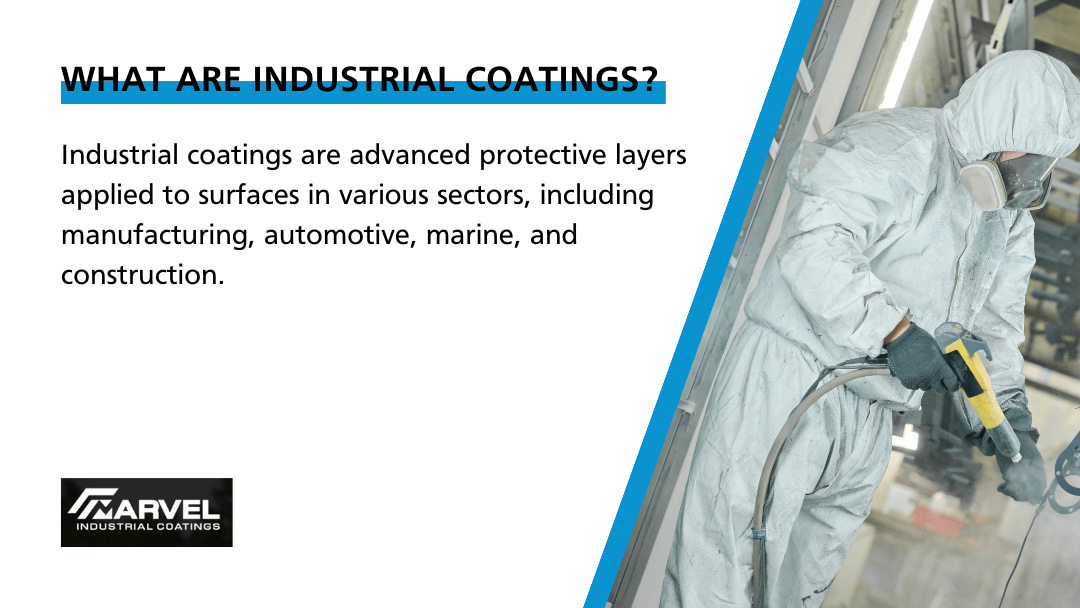
What Happens if You Apply Industrial Coatings in Cold Weather?
Applying industrial coatings in conditions that are too cold can lead to several detrimental outcomes. At lower temperatures, the viscosity of the coating increases, making it more difficult to apply evenly. This can result in an uneven coating thickness, compromising the aesthetic quality and affecting the coating's protective capabilities. Moreover, cold weather significantly slows down the curing process. Inadequate curing can lead to a lack of adhesion, causing the coating to peel or blister over time. Additionally, moisture in the air during cold conditions can become trapped within the coating layer, leading to premature corrosion and diminished coating lifespan. These problems highlight the importance of adhering to the recommended temperature guidelines for applying industrial coatings to ensure their effectiveness and durability.
Application Considerations
Ambient Temperature: A Key Factor
The ambient temperature during the application can make or break the effectiveness of a coating. Optimal conditions usually fall between 50°F and 90°F.
Challenges Below Optimal Range: Slow curing, risk of sagging, and poor adhesion.
Challenges Above Optimal Range: Quick drying leading to uneven application.
Surface Temperature
The temperature of the surface itself is critical. Deviations can lead to poor curing and reduced longevity.
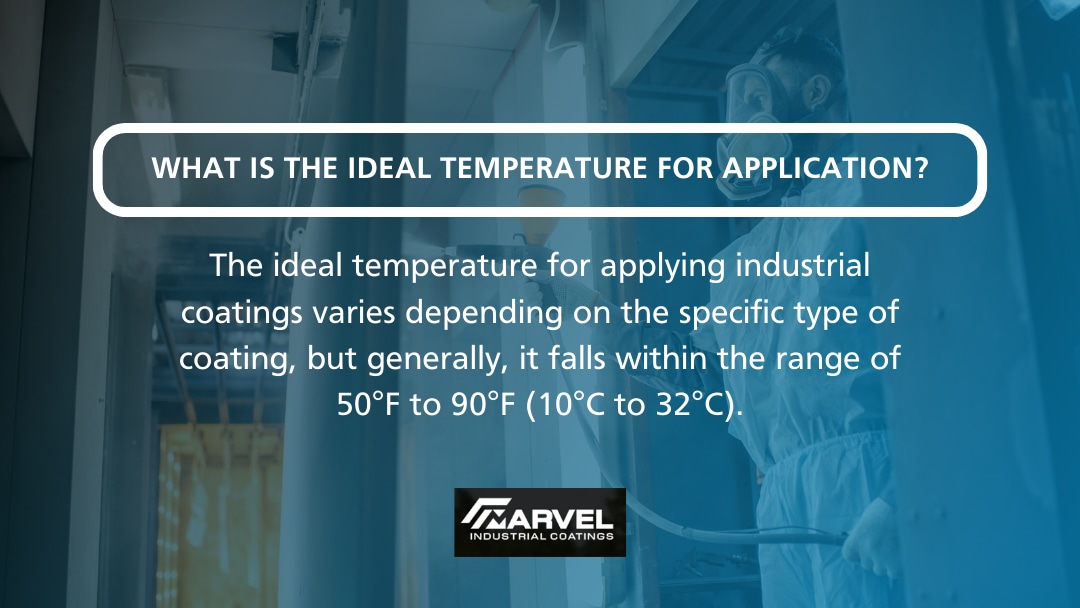
Post-Application Performance
Adapting to Thermal Expansion
Coatings must endure the substrate's expansion and contraction with temperature changes. Inflexible coatings may crack or delaminate. As temperatures fluctuate, materials expand and contract at varying rates. This natural physical response can place significant stress on the coating. If a coating lacks sufficient flexibility, it cannot accommodate these dimensional changes in the substrate, leading to potential structural failures.
High-Temperature Environments
Applying industrial coatings in excessively hot conditions can cause problems that compromise the coating's integrity and performance. High temperatures often rapidly reduce the coating's viscosity, making it too thin and challenging to control during application. This can result in uneven layers with poor thickness control, negatively impacting both protective qualities and appearance. Additionally, hot weather accelerates the drying process, which might seem advantageous, but it actually prevents the coating from adhering properly to the surface. This inadequate adhesion can lead to peeling or flaking over time. Moreover, the rapid drying can trap solvents or air within the coating, forming bubbles or blisters and further weakening the coating. These issues underscore the necessity of applying industrial coatings within the recommended temperature range to ensure optimal adhesion, curing, and long-term durability.
Maintaining Corrosion Resistance
Maintaining corrosion resistance in extreme temperatures is vital for the longevity of the substrate.
Choosing the Right Coating
Assessing the Environment
Understanding the environmental conditions, including temperature extremes, is crucial for selecting an appropriate coating.
Matching Coating to Temperature
Select coatings designed to withstand the specific temperature range of the application area.
Maintenance and Inspection: Ensuring Longevity
Regular maintenance and inspection are critical, especially in fluctuating temperatures.
Maintenance Strategies
Frequent Cleaning: Essential for removing harmful debris.
Routine Inspections: Crucial for early detection of problems.
Prompt Repairs: It is necessary to prevent minor issues from worsening.
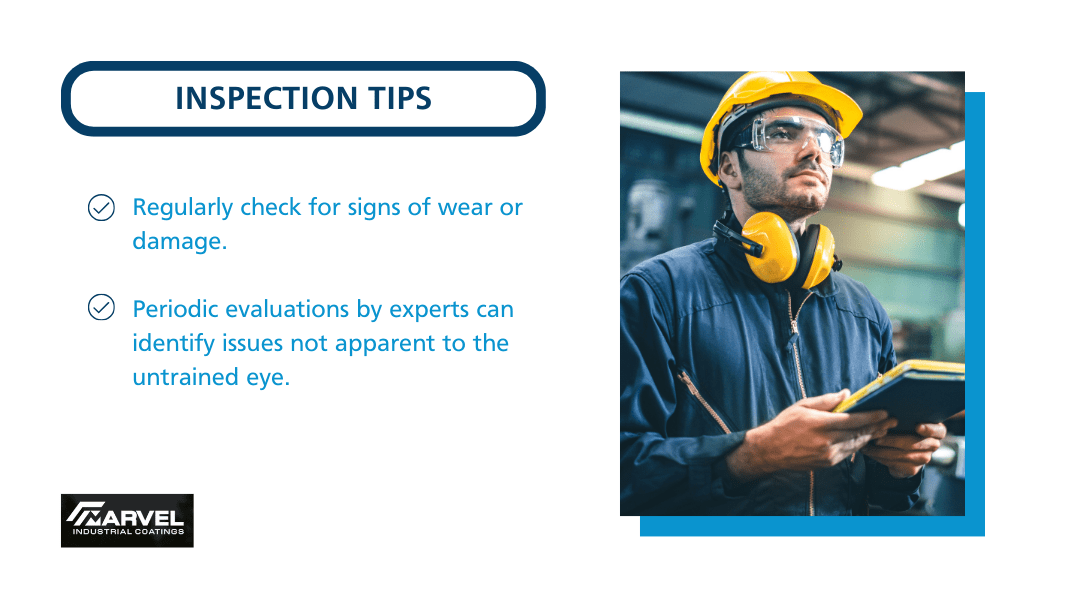
Inspection Tips
Visual Inspections: Regularly check for signs of wear or damage.
Professional Assessments: Periodic evaluations by experts can identify issues not apparent to the untrained eye.
Advanced Considerations
Technological Innovations
New coatings are constantly being developed to withstand extreme temperatures and environmental conditions better.
Environmental and Regulatory Compliance
Selecting coatings that meet environmental and safety regulations is increasingly important in today's industry.
Cost-Benefit Analysis
While some high-performance coatings may be more expensive upfront, their longevity and protective qualities can offer long-term savings.
Conclusion
The interplay between temperature and industrial coatings is critical to their application and performance. By understanding and respecting this relationship, industries can ensure the durability and effectiveness of their coatings, leading to prolonged lifespan of their assets and often resulting in considerable cost savings and enhanced safety.
Why Choose Marvel Coatings for Industrial Coating Products?
When it comes to industrial coatings, trust matters. Marvel Coatings offers top-notch solutions that prioritize safety and quality. With a track record of excellence, quality technology, and a commitment to environmental responsibility, Marvel Coatings has earned the trust of countless businesses. Contact Marvel Coatings today to request a quote and discover how our expertise can enhance your project while ensuring the utmost safety and quality. Your satisfaction is our priority.