Comparing Industrial Floor Coatings: Which One is Right for You
When it comes to protecting and enhancing industrial floors, the right coating can make all the difference. Industrial environments are often subjected to heavy foot traffic, machinery, chemical spills, and other challenges that demand durable and resilient flooring solutions. With a variety of options available, choosing the right industrial floor coating can be an intimidating task. In this blog, we'll compare the most common types of industrial floor coatings to help you determine which one is right for your facility.
1. Polyurea Coatings
Overview:
Polyurea coatings are rapidly gaining recognition as one of the top-performing industrial floor solutions. These coatings are known for their exceptional flexibility, quick curing times, and superior resistance to a wide range of environmental and chemical challenges. Unlike traditional coatings, polyurea offers an unparalleled combination of durability, adaptability, and speed of application, making it a preferred choice for modern industrial environments.
Benefits:
Extreme Durability:
Polyurea coatings offer superior resistance to abrasion, impact, and heavy loads, ensuring a long-lasting surface that can withstand the toughest industrial conditions. This makes them ideal for facilities that experience constant wear and tear.Rapid Curing Time:
One of the standout features of polyurea is its incredibly fast curing time, often within minutes, allowing for minimal downtime during installation. This is crucial for facilities that need to maintain operations without significant interruption.Chemical and Stain Resistance:
Polyurea coatings are highly resistant to a wide range of chemicals, including oils, solvents, and acids. This makes them an excellent choice for facilities where chemical spills are a concern, ensuring the floor remains protected and easy to clean.Flexibility and Crack Resistance:
The elasticity of polyurea allows it to expand and contract with temperature changes, reducing the likelihood of cracks and damage. This flexibility makes polyurea ideal for environments with frequent temperature fluctuations or where structural movement is common.UV Stability:
Unlike many other coatings, polyurea is UV-stable, meaning it won’t yellow or degrade when exposed to sunlight. This makes it an excellent option for both indoor and outdoor applications where long-term appearance is important.
Considerations:
Cost:
Polyurea coatings can be more expensive than some other options, but their long-term durability and performance often justify the initial investment.Installation Expertise:
Due to the rapid curing time and specific application techniques required, professional installation is crucial to ensure optimal performance.
Best For:
Warehouses, manufacturing plants, chemical processing facilities, food processing plants, and any environment where rapid application, extreme durability, and chemical resistance are critical.
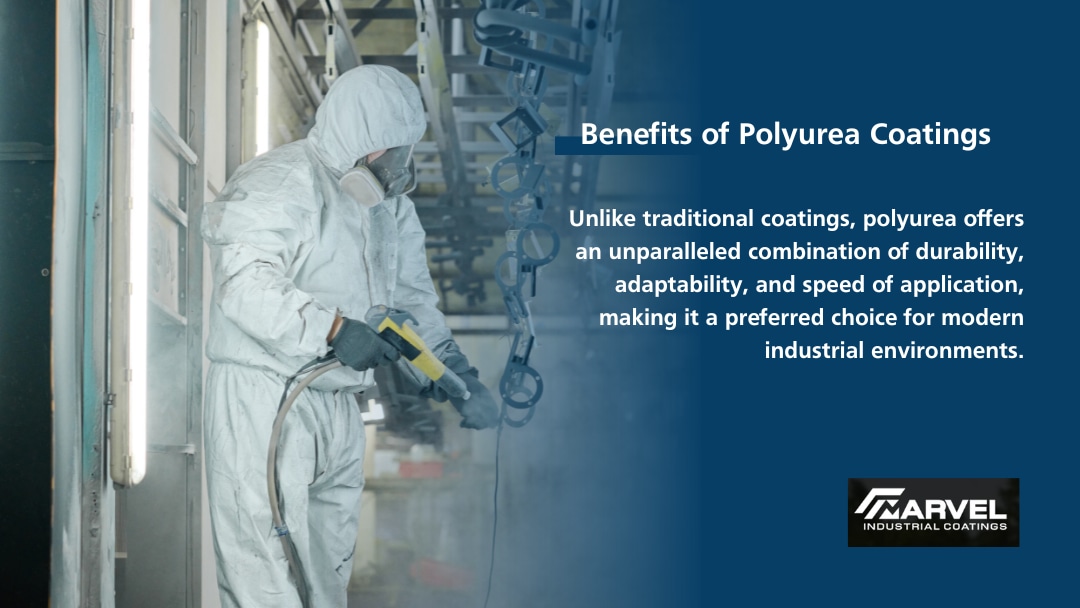
2. Epoxy Coatings
Overview: Epoxy coatings are one of the most popular choices for industrial flooring. Composed of resins and hardeners, epoxy forms a tough, durable surface that can withstand heavy loads and resist chemicals.
Benefits:
Durability: Epoxy coatings offer exceptional durability and can handle high levels of foot and vehicular traffic, making them ideal for warehouses, factories, and garages.
Chemical Resistance: This coating is highly resistant to chemicals, oils, and solvents, which is crucial for facilities like chemical plants and laboratories.
Aesthetic Appeal: Available in a wide range of colors and finishes, epoxy can enhance the appearance of your facility, providing a clean and polished look.
Ease of Maintenance: Epoxy floors are easy to clean and maintain, requiring only regular sweeping and occasional mopping.
Considerations:
Installation Time: Epoxy coatings require a multi-step installation process, including surface preparation, primer application, and curing time. This can result in longer downtime for your facility.
Temperature Sensitivity: Epoxy may not be the best choice for environments with extreme temperature fluctuations, as it can become brittle and crack.
Best For: Warehouses, manufacturing plants, automotive shops, and facilities with high chemical exposure.
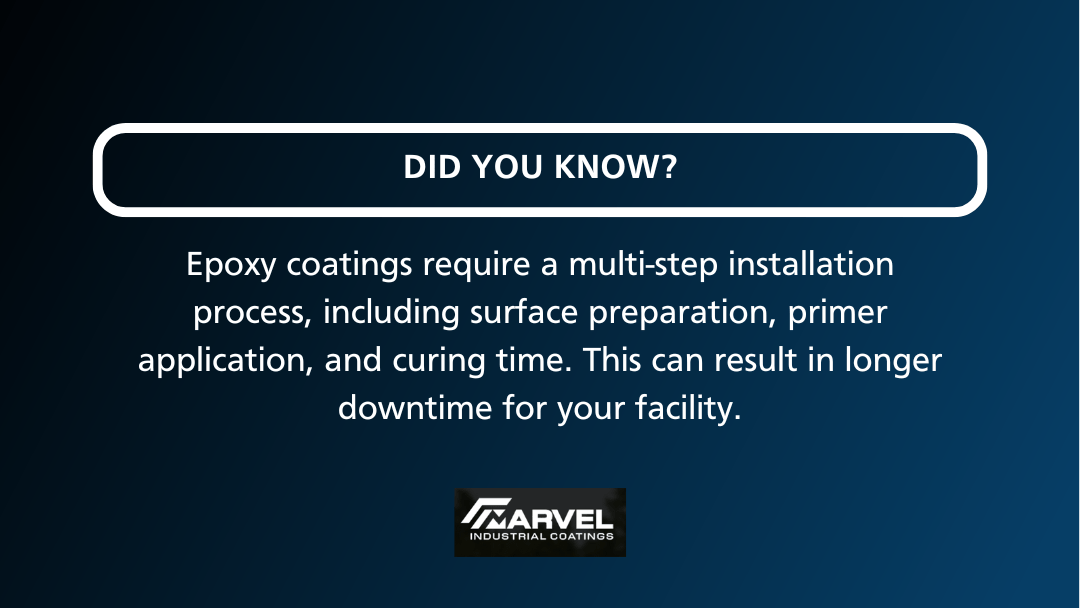
3. Polyurethane Coatings
Overview: Polyurethane coatings are known for their flexibility and resistance to abrasion. Unlike epoxy, polyurethane coatings are more elastic, making them suitable for environments with frequent temperature changes.
Benefits:
Flexibility: The elasticity of polyurethane allows it to expand and contract with temperature changes, reducing the likelihood of cracks.
Abrasion Resistance: Polyurethane coatings offer excellent resistance to scratches, scuffs, and general wear and tear, making them ideal for high-traffic areas.
UV Stability: Unlike epoxy, polyurethane is UV-stable, meaning it won't yellow or fade when exposed to sunlight, making it a great option for facilities with large windows or outdoor areas.
Chemical Resistance: Polyurethane provides good resistance to a variety of chemicals, although it may not be as resistant as epoxy in highly corrosive environments.
Considerations:
Cost: Polyurethane coatings are generally more expensive than epoxy, which may be a factor for budget-conscious projects.
Softer Surface: While flexible, polyurethane is also softer than epoxy, which can lead to denting or gouging under heavy loads.
Best For: Food processing plants, warehouses with outdoor exposure, retail spaces, and environments with fluctuating temperatures.
4. Polished Concrete
Overview: Polished concrete is a durable and low-maintenance flooring option created by grinding down the surface of a concrete slab to achieve a smooth, reflective finish. This coating-free option is gaining popularity for its minimalistic and modern aesthetic.
Benefits:
Longevity: Polished concrete is extremely durable and can last for decades with minimal maintenance.
Low Maintenance: With no coatings to wear off or need reapplication, polished concrete is easy to maintain with regular cleaning.
Cost-Effective: While the initial polishing process can be costly, the long lifespan and low maintenance requirements make polished concrete a cost-effective option over time.
Eco-Friendly: Polished concrete utilizes the existing concrete slab, reducing the need for additional materials, which makes it an environmentally friendly option.
Considerations:
Limited Aesthetic Options: While polished concrete can be stained or colored, the aesthetic options are more limited compared to epoxy or polyurethane coatings.
Surface Hardness: The hard surface of polished concrete can be tough on foot traffic, potentially leading to discomfort in areas where employees stand for long periods.
Susceptible to Stains: Although polished concrete is sealed, it can still be susceptible to staining from spills if not cleaned promptly.
Best For: Warehouses, distribution centers, showrooms, and environments where a modern, industrial look is desired.
5. MMA (Methyl Methacrylate) Coatings
Overview: MMA coatings are fast-curing floor solutions that offer exceptional durability and chemical resistance. These coatings are ideal for facilities that need minimal downtime during installation.
Benefits:
Rapid Installation: MMA coatings cure quickly, often within just a few hours, allowing facilities to return to operation almost immediately.
Cold-Temperature Application: MMA can be applied in cold environments, even below freezing, making it ideal for cold storage facilities and freezers.
Durability: MMA coatings offer excellent resistance to chemicals, impact, and abrasion, making them suitable for demanding environments.
Customizable: Available in a variety of colors and finishes, MMA coatings can be tailored to meet specific aesthetic and functional requirements.
Considerations:
Odor: MMA coatings emit a strong odor during application, which requires proper ventilation and may necessitate temporary evacuation of the facility.
Cost: The cost of MMA coatings can be higher than other options due to the specialized materials and installation process.
Best For: Cold storage facilities, food and beverage processing plants, pharmaceutical manufacturing, and any facility requiring rapid installation.
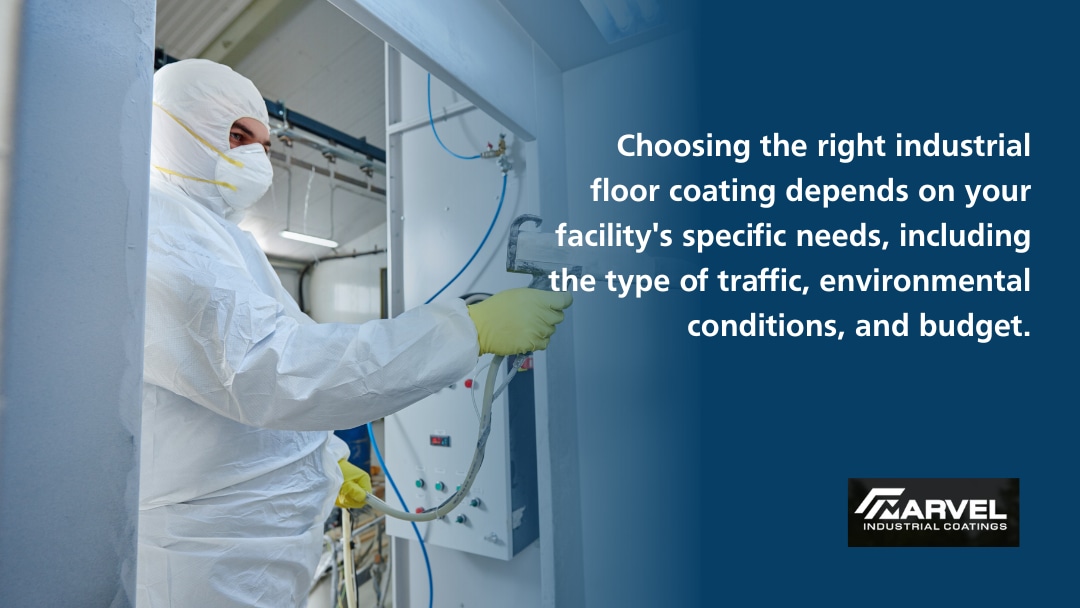
Choosing the right industrial floor coating depends on your facility's specific needs, including the type of traffic, environmental conditions, and budget. Epoxy and polyurethane offer excellent durability and chemical resistance, while polished concrete provides a cost-effective, low-maintenance option with a modern aesthetic. MMA coatings, with their rapid installation and durability, are ideal for facilities that cannot afford extended downtime.
By understanding the benefits and limitations of each option, you can make an informed decision that will enhance the longevity and performance of your industrial floors.